RAAC Panels – The Silent Threat Lurking Above
In the world of construction, some dangers are concealed, lurking high above our heads.
Reinforced Autoclaved Aerated Concrete (RAAC) panels, once hailed for their thermal efficiency and fire resistance, have now become a cause for concern.
Today, I’m sitting down with our Managing Director, John Staves, to shed light on the risks associated with RAAC panels and discuss potential solutions for those who find themselves in the shadow of this hidden peril.
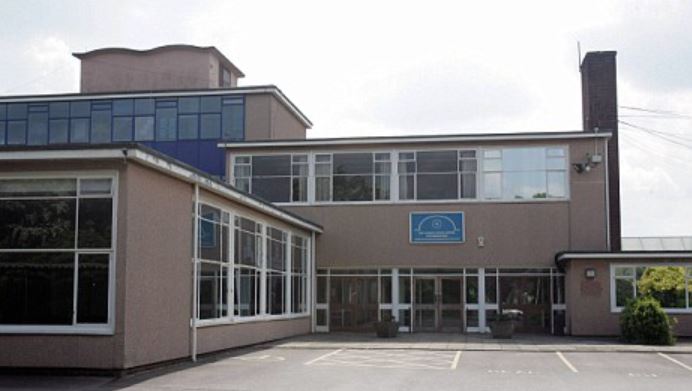
A Relic from the Past
RAAC panels emerged as a construction method of choice during the 1960’s and 1970’s primarily used in public buildings like schools, hospitals, and corporate structures. These panels found their niche as roofing materials due to their lightweight nature and excellent fire-resistant properties.
The Singlewell Primary Wake-Up Call
The alarm bells began to ring when part of the ceiling at Singlewell Primary School in Kent collapsed on a weekend in 2018. Thankfully, no one was harmed, but this incident underscored the urgent need for action in dealing with the potential dangers of RAAC.
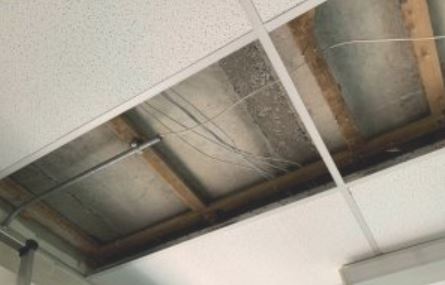
Unseen and Unaware
Many schools and building owners remain blissfully unaware that RAAC panels make up their roofs. The general assumption that concrete roofs are structurally sound has left these hidden time bombs unchecked.
The crisis we face today is partly due to the prolonged use of RAAC panels and inadequate maintenance over the years.
RAAC Concrete panels. Image credits: New Civil Engineer
The Silent Threat
RAAC panels are not like typical concrete structures that give warning signs of impending failure through stress cracks. Instead, they are highly porous, prone to deflections, cracks, and structural weaknesses. Failure in RAAC panels can be attributed to various factors, including manufacturing defects, suboptimal original designs, and moisture ingress.
The Role of Moisture Ingress
Moisture ingress is a particularly insidious problem with RAAC panels, especially when they serve as roofing material. Over time, weatherproof membranes, such as asphalt, deteriorate, allowing moisture to infiltrate the panels. This moisture corrodes the reinforcement within, weakening the bond with the concrete and eventually leading to failures in the panels.
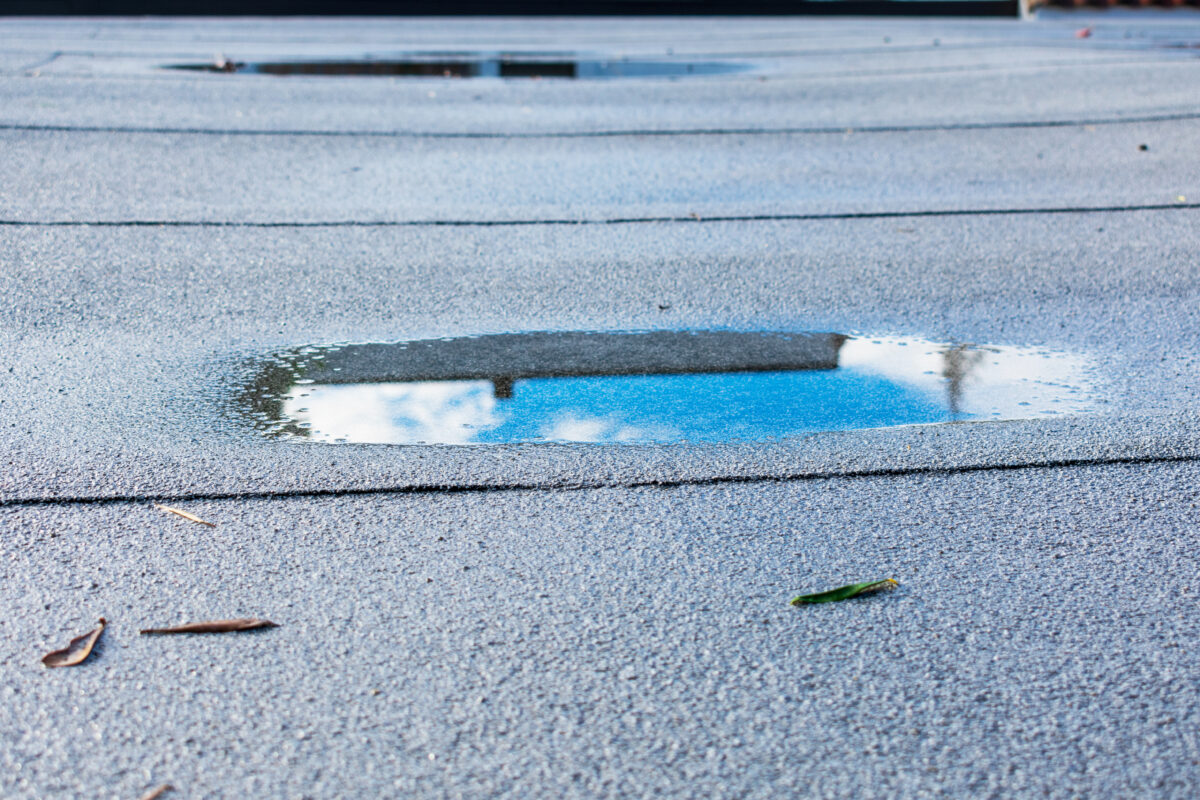
Identifying RAAC Panels
To determine if a building contains RAAC panels, a visual inspection is the first step. Competent structural engineers look for telltale signs such as panel width, span, and edge details. If suspicions persist, core sampling can be employed to confirm the presence of RAAC.
The Next Steps
If RAAC is confirmed, immediate actions are crucial. Affected areas should be cordoned off, and temporary propping may be necessary to prevent collapse. Depending on the severity, options include the removal and replacement of panels or the addition of a new structural layer beneath them.
The priority is to ensure the safety of the occupants below.
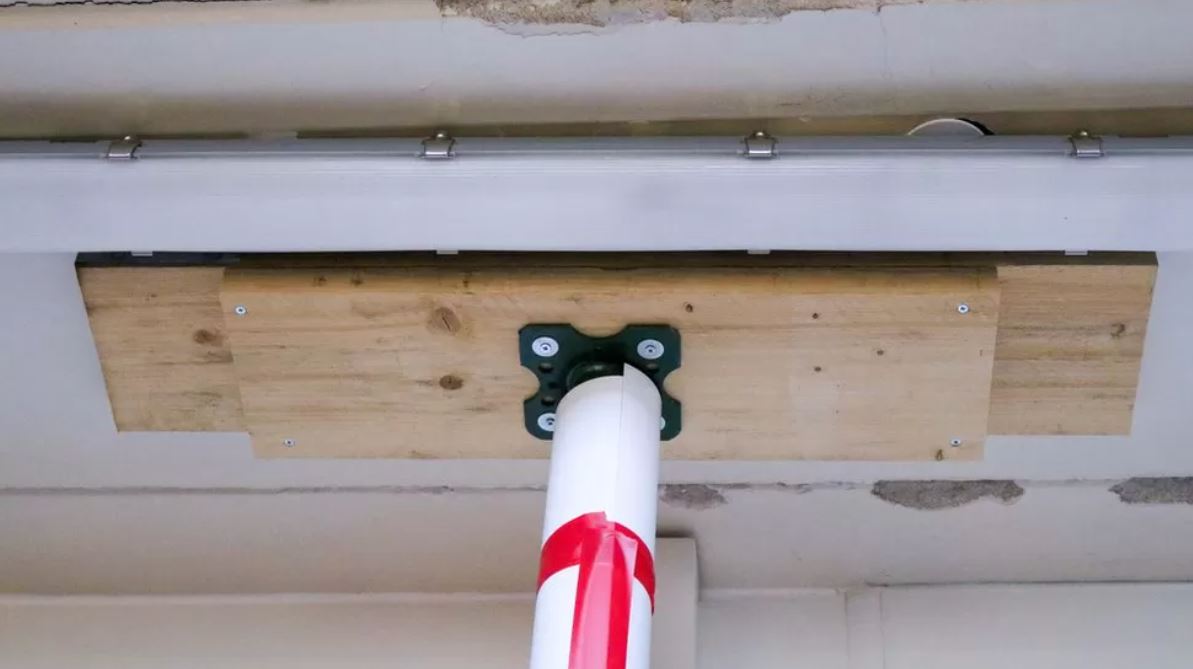
Ceiling support at Queen Elizabeth Hospital in King’s Lynn, Norfolk
Strengthening Bearing Support
Another consideration is reinforcing the bearing points to alleviate stress on the RAAC panels. This can involve extending support to where the reinforcement lies within the panels.
Seeking Guidance
For those grappling with RAAC-related concerns, the Department of Education has issued a guidance document in 2022, updated in August 2023, titled “Reinforced Autoclaved Aerated Concrete (RAAC): Identification guidance.” This resource provides valuable information for identifying and addressing RAAC-related issues.
Conclusion
In conclusion, RAAC panels are a hidden danger that can fail without warning. Awareness and proactive inspections are essential to ensure the safety of occupants in buildings constructed with RAAC panels. By following guidelines and seeking expert advice, we can mitigate the risks associated with this silent threat that looms above our heads. Your safety and the structural integrity of your building depend on it.
Do you suspect RAAC in your building? Contact us for expert advice
Contact Me