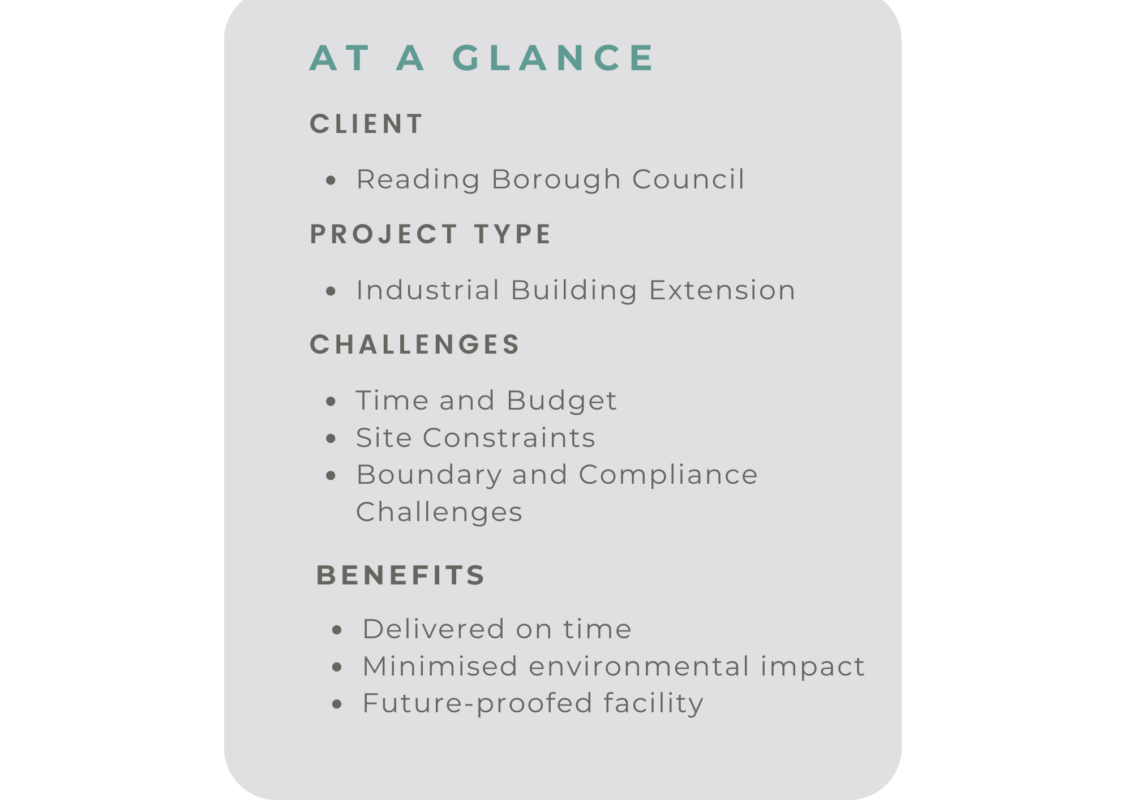
Project Overview
Reading Borough Council sought to expand their vehicle workshops at Bennet Road, where they service and maintain refuse vehicles. This extension was crucial as the Council had begun transitioning their fleet to electric vehicles (EVs).
The existing workshop facilities were too small to accommodate these larger, more complex vehicles and required additional space for future maintenance needs. The objective was not only to extend the workshops but also to future-proof the facilities for the Council’s evolving fleet.
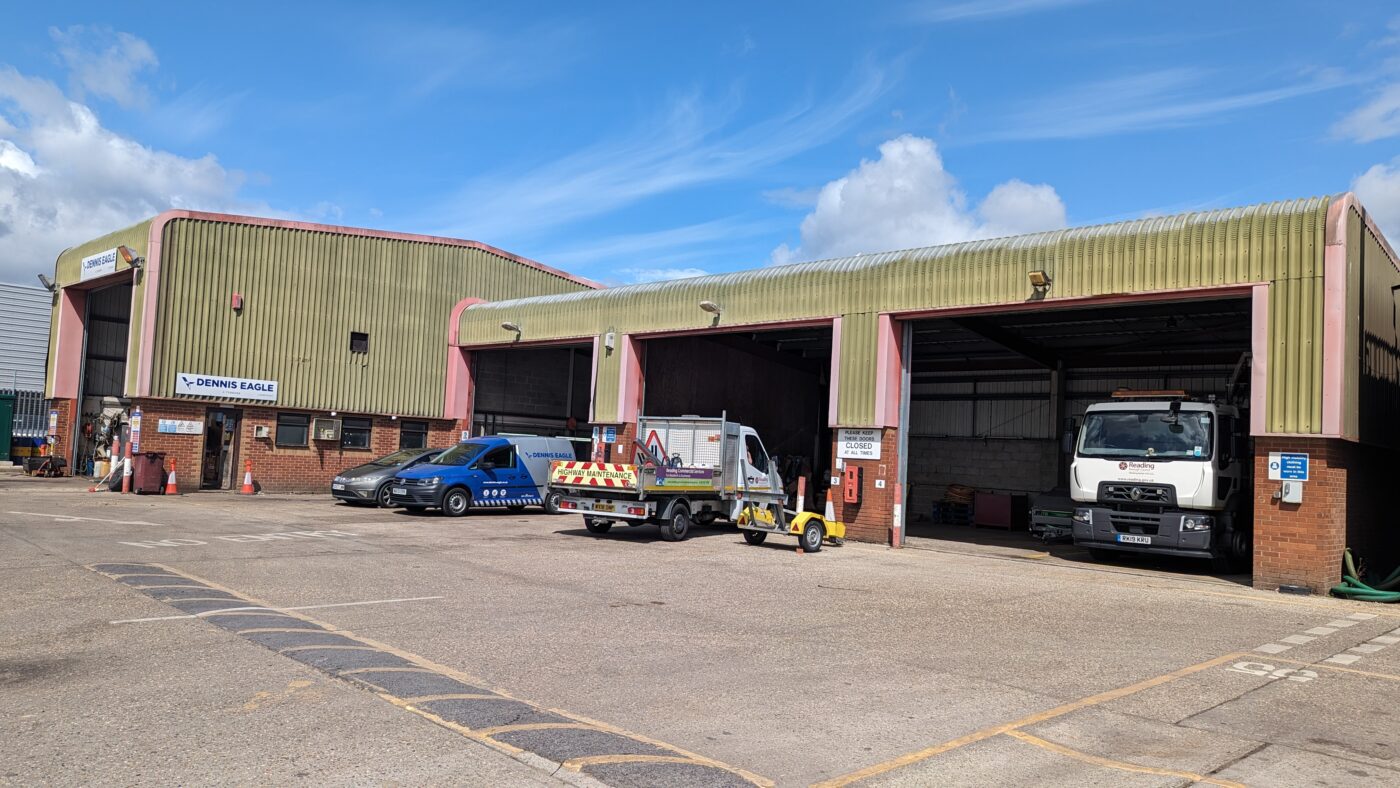
Existing warehouse facility at Bennet Road, Reading
Key Objectives
The primary goal was to extend the height and depth of the existing workshop, providing ample space to accommodate the new EVs and ensuring efficient future maintenance. The Council was under significant time pressure and required the expanded facility to be fully operational by September 2024.
We were appointed in the summer of 2023, with the challenge of taking the project from planning approval to site construction and completion within a tight 15-month window.
Unique Challenges & Constraints
1. Time and Budget Pressure
The timeline was critical, as the Council needed the new facility open and functioning by September 2024. The initial budget was set low, and we advised the client early on that this might be insufficient. Cost-saving measures were prioritised, focusing on sustainable solutions that aligned with the client’s environmental goals.
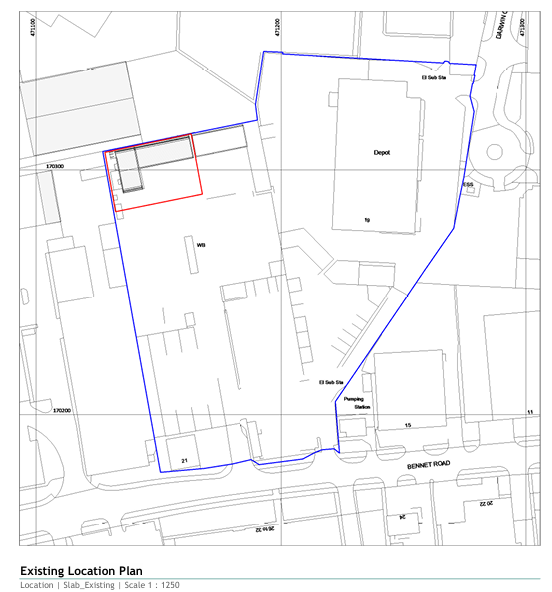
2. Site Constraints
The workshop is located on a busy, operational site. We needed to maintain smooth traffic flows for refuse vehicles while constructing the extension in a rear corner of the property.
One of the workshops remained operational throughout the construction process, with alternative offsite provisions made by the Council.
3. Boundary & Compliance Challenges
The project site was very close to the property boundary, necessitating detailed fire safety considerations for the new cladding.
Although the existing building did not meet current standards, we had to bring the entire structure up to building regulations, a challenge that significantly increased costs.
One area that needed improvement was the fire safety measures. Building Control required a fire refuge to be added on the first floor. The ground floor was already fully compliant with the Disability Discrimination Act (DDA), ensuring accessibility for office staff and visitors.
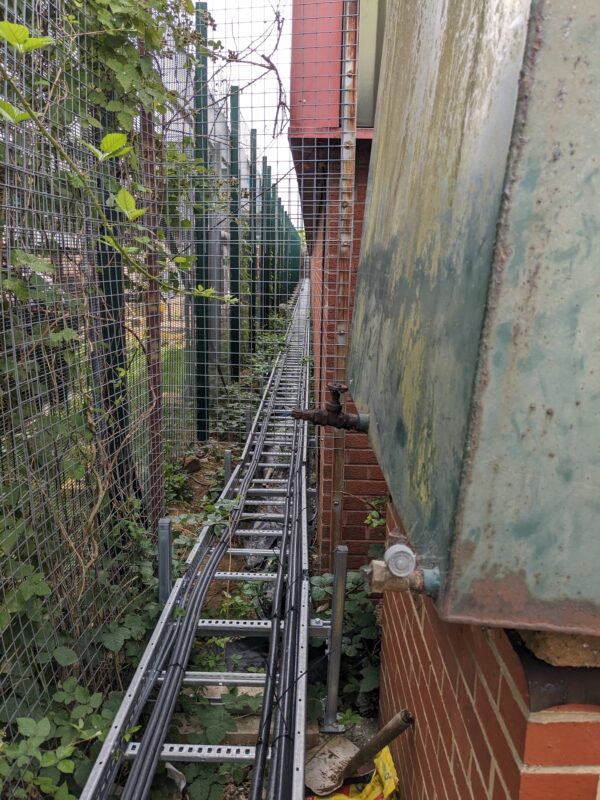
Tight rear boundary
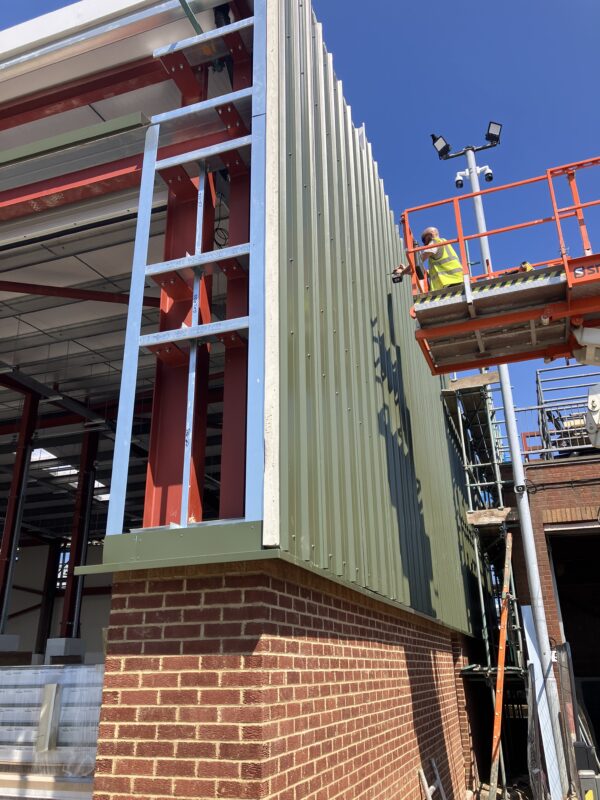
Cladding going in
Structural & Engineering Solutions
1. Reuse of Existing Structures
To stay within budget and maintain sustainability, we reused as much of the existing structure as possible.
The original steel frame was retained and extended both vertically and horizontally to accommodate the new height requirements and additional bays.
The yard’s existing 250mm thick concrete slab was also reused, screeded over to integrate it seamlessly with the new floor plan. This approach eliminated the need for a new ground floor slab, significantly reducing costs and environmental impact.
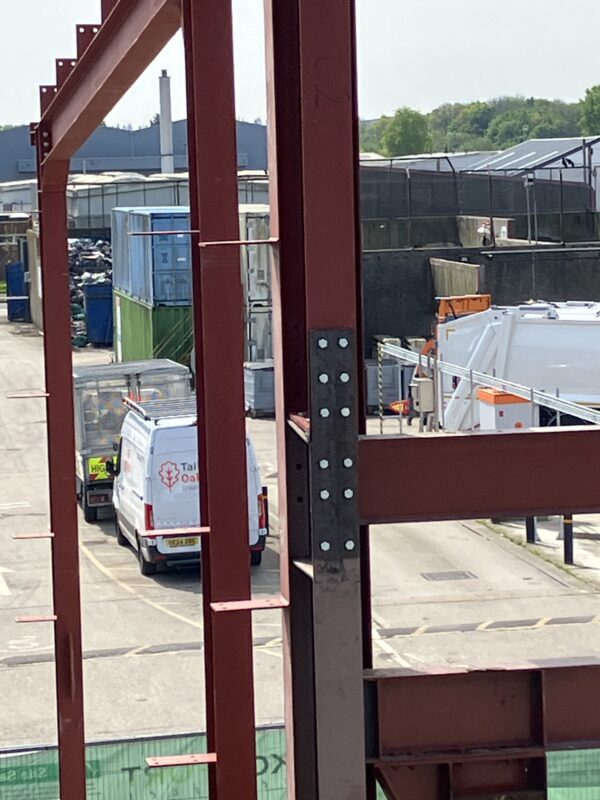
Frame extended upwards to increase headroom
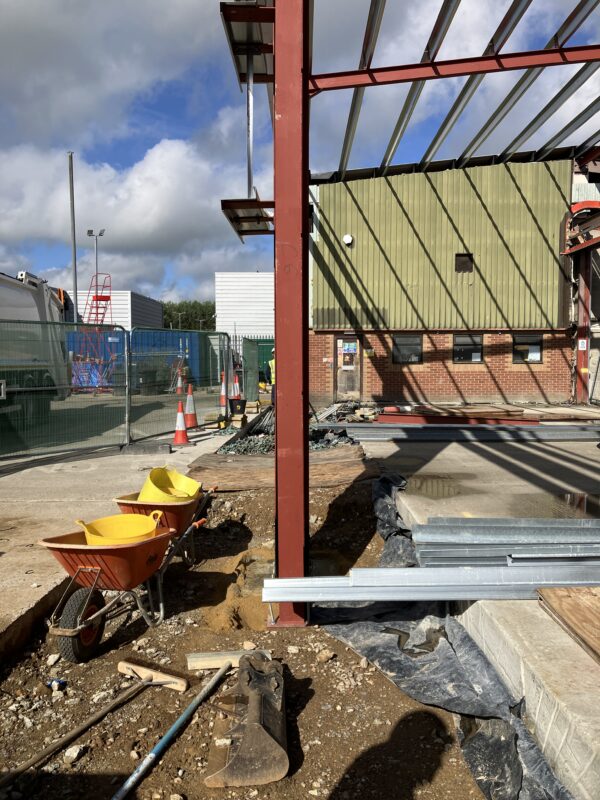
Slab out to allow new ramped entrance to be formed
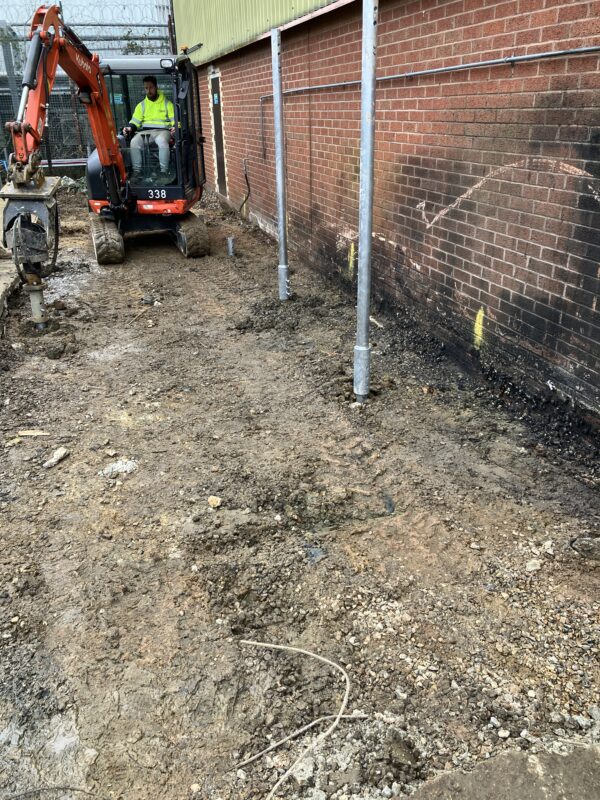
2. Screw Piles
The decision to use screw piles for the foundations was a pivotal solution that saved both time and money.
Traditional excavation would have risked disturbing potentially contaminated soil on the refuse site, requiring expensive removal and disposal.
By using screw piles, we minimised digging and avoided disturbing the ground, thus cutting costs and adhering to environmental best practices.
3. Sustainability Focus
Sustainability was a driving factor throughout the project. In addition to reusing the structural frame and floor slab, we used high-efficiency, insulated cladding and installed roller shutter doors with built-in insulation.
These elements exceeded standard building regulation requirements, as per the Council’s brief to create a comfortable working environment for their technicians while improving energy efficiency.
4. Architectural & Engineering Coordination
The project required intricate coordination between the structural and service designs, which we managed through advanced software tools like Revit.
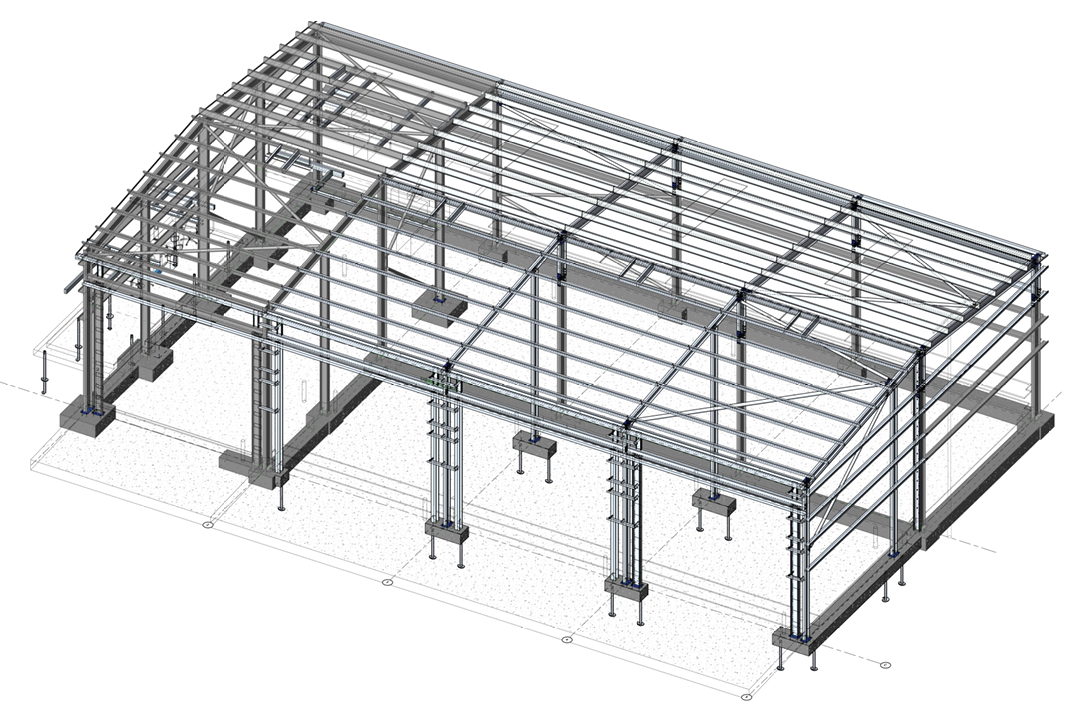
This allowed us to integrate third-party services into our structural framework seamlessly and avoid design-related issues during construction.
This technology was crucial in coordinating complex elements, such as integrating heating systems that were controlled by the roller shutter doors to ensure no heat was wasted when the doors were open.
Overcoming Project Hurdles
Phased Construction Delays
The project was originally divided into two phases to ensure two workshop bays could be handed back early while the rest of the extension was completed.
However, due to site proximity issues—particularly the inability to gain permission from neighbouring properties to access their land—the planned phasing had to be overhauled. This caused a delay in handing over the initial two bays but did not impact the final deadline for the entire building.
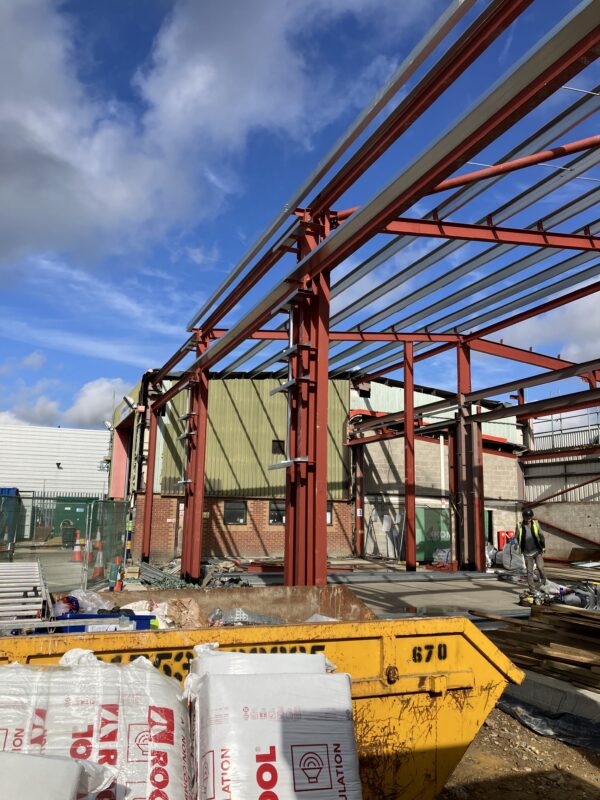
New frame in!
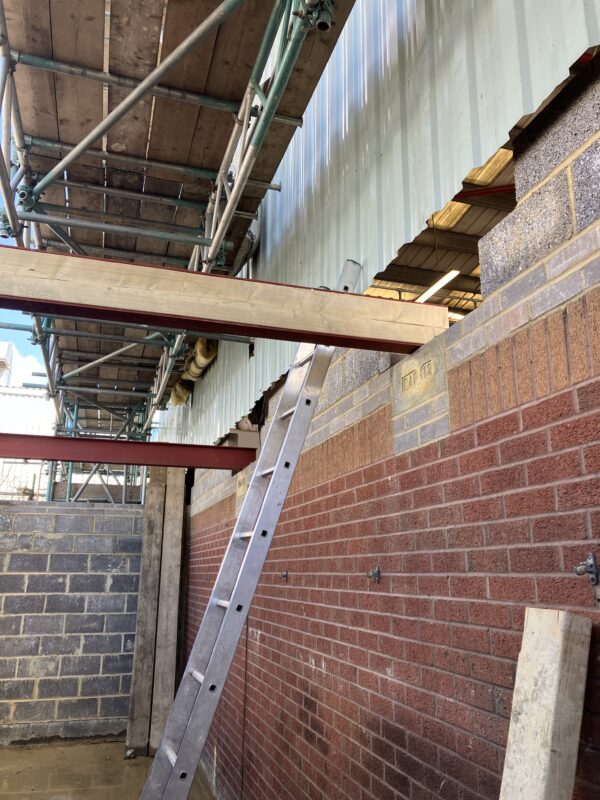
Office annex roof, beams going in
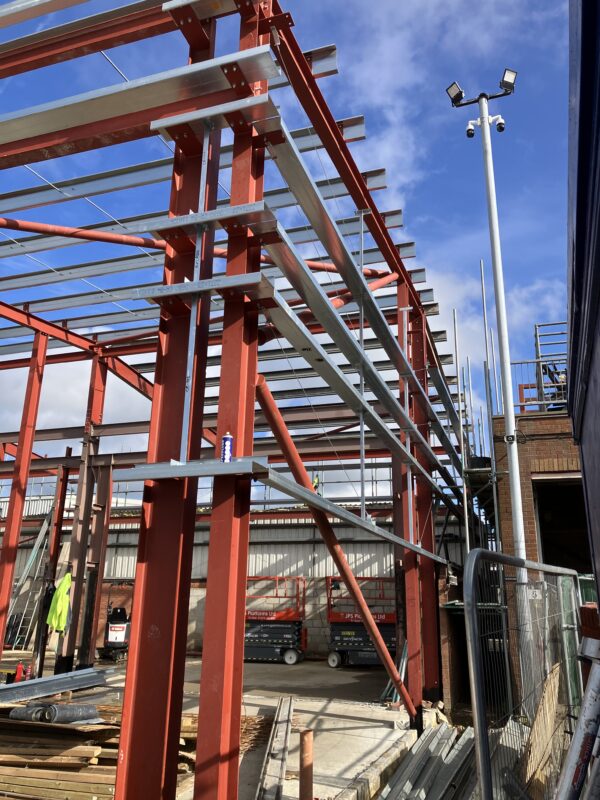
Budget Adjustments
Despite the initial cost-saving measures, the best tender came in 20% over the original budget due to material costs and additional compliance requirements.
The budget continued to rise, eventually reaching 1.5 times the original due to increased client specifications for fixtures, fittings, and office space requirements.
Conclusion
The Bennet Road workshop extension project successfully met its objectives of expanding Reading Borough Council’s maintenance facilities to accommodate their growing fleet of electric vehicles.
Through strategic reuse of existing structures, innovative foundation solutions, and sustainable building practices, we were able to minimise costs and environmental impact while delivering a state-of-the-art facility. Although there were significant challenges, including tight deadlines, budget adjustments, and compliance hurdles, the project remained on track for completion by September 2024.
The Council now has a future-proofed facility that not only serves their current needs but is also prepared for the growing demands of their electric vehicle fleet.
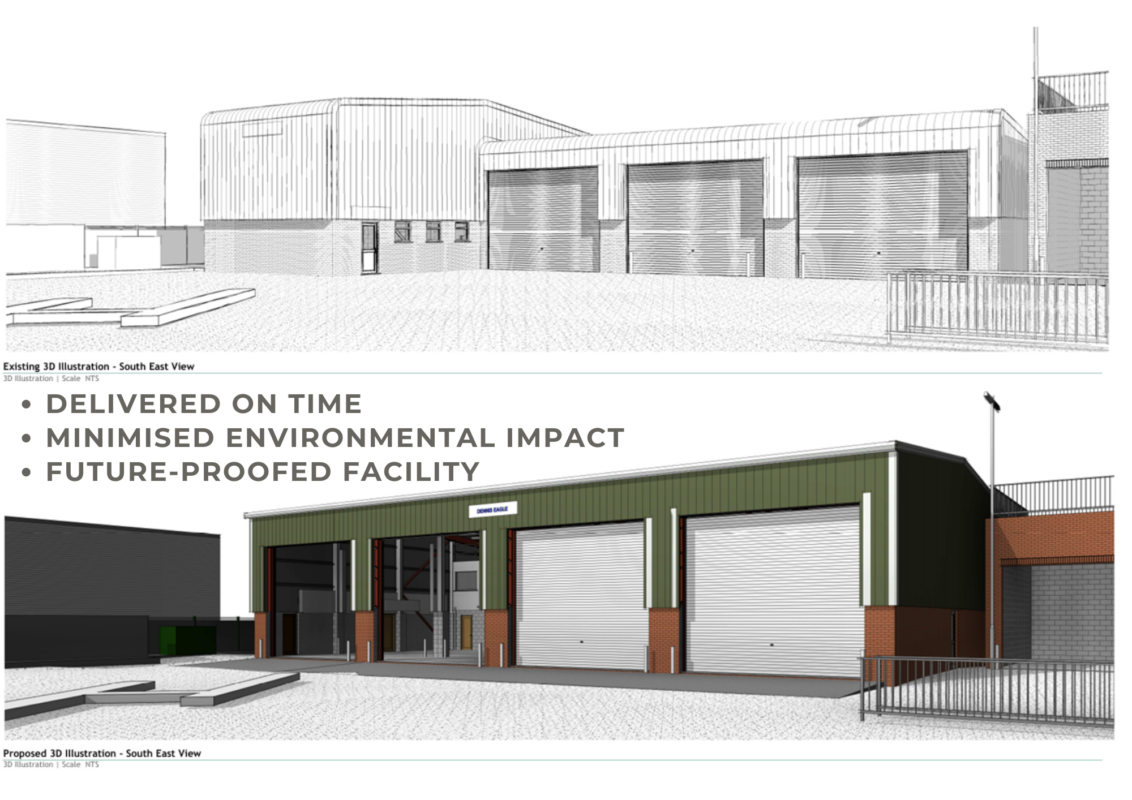